Hardening and Tempering with Induction
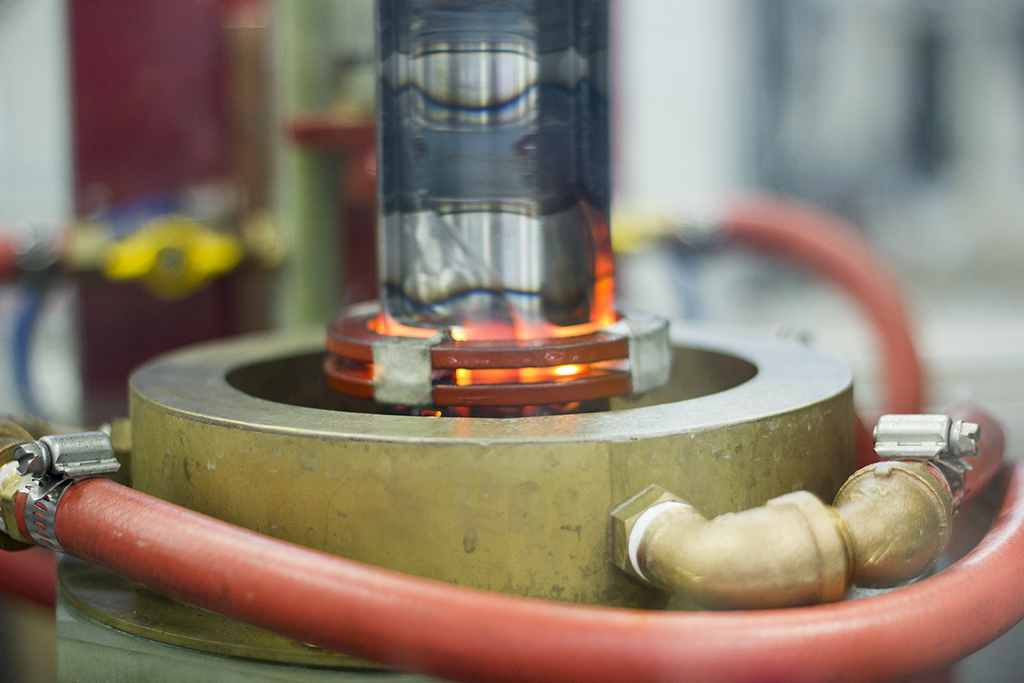
What is Hardening?
Hardening can be defined simply as any process by which the hardness of a material is increased and ductility is decreased. This process is employed to reinforce surfaces prone to high wear and enhance the overall longevity of parts. While various hardening methods exist, each with its suitability depending on the material, Induction technology is frequently applied in a specific hardening process known as Quenching and Tempering.
What is Quenching & Tempering?
Quenching and Tempering constitute a hardening process exclusively applicable to medium to high-carbon steel. Initially, the steel undergoes heating to a sufficiently high temperature, causing a transformation in the crystal structure from ferrite to austenite. In this altered state, the steel can absorb a higher amount of carbon than under normal circumstances. Subsequently, the steel is rapidly quenched using water, oil, or a water-polymer solution in induction equipment. This rapid cooling prevents the formation of carbon precipitates that could compromise the final hardness of the steel.
As the steel cools to a lower temperature, it attempts to revert to its original low-temperature state. However, having absorbed more carbon than its original state can accommodate, the steel transforms into a distinct crystal structure known as martensite. Martensite is exceptionally hard due to its distorted crystal structures and elevated carbon saturation. While the steel achieves high hardness at this point, it also becomes quite brittle.
Tempering is the subsequent step, involving reheating the steel to a lower temperature to slightly reduce hardness and, consequently, brittleness. The specific temperature for tempering depends on the desired hardness level. Once the target hardness is attained, the steel undergoes another quenching process to prevent any residual heat from further tempering the steel.
Quenching & Tempering with Induction
Induction technology is predominantly employed in Quenching and Tempering procedures, where it offers notable advantages. Achieving the desired hardness profile in this procedure demands exceptional precision in both the heating and quenching of the steel. Even slight variations, such as heating for a moment too long or quenching at an incorrect temperature, can lead to significant disparities from one part to another. Hence, maintaining precise control over the process becomes crucial, and induction technology stands out by providing superior control compared to other heating methods.
The automatic handling and fixturing of components for heating and quenching contribute to high production rates and consistent results across various parts. Induction stands out as the fastest method for hardening and heat treating, resulting in minimal distortion, no surface decarburization, a fine-grain microstructure, and meticulously controlled hardness patterns. For any facility aiming to elevate production to the next level, induction emerges as the ideal solution.
Induction Case Hardening
Selective induction case hardening can enhance the performance of parts by providing hybrid mechanical properties, hardness where needed on wear surfaces, and ductility in the core to provide impact resistance.
Selective induction hardening has the ability to specifically target and apply heat rapidly to a localized area of a part. As a result, the part develops a layer, or case, of hardened material. This is ideal for parts that are highly stressed in operation and require a combination of mechanical properties. For example, high yield strength, fatigue resistance, and resistance to wear at the same time.
The precise hardness pattern can be controlled by appropriate adjustment of the frequency used, induction coil geometry, power level, and the location of the part in the coil. The hardness pattern remains highly consistent from part to part due to industry-leading precision in Radyne systems. Rotation during heating assures a uniform case.
Progressive Induction Hardening | Induction Scanning
Frequently, parts require surface hardening in selected areas to provide optimum performance and long service. Induction hardening, using progressive heating and quenching, provides an economical way to process shafts or other parts.
By progressively passing a steel shaft through a heating coil into a water quench, the outer skin can be heated, quenched, and hardened without affecting its core. When a completely uniform case is required it is often necessary to rotate the shaft. The coil and the associate water quench usually form one unit, as the position of the water quench with respect to the inductor is very important. The water supply is often fed through the coil itself, as illustrated. Controlled scanning of shafts through the induction coil and quench ring while rotating produces controlled case depths over adjustable lengths of the shafts, all in on an automated cycle.
Control of the case depth depends upon the power input from the generator and the downward speed of the shaft through the induction coil while the length of the hardened section is controlled by a pyrometer which is set to suit specifications. Once the desired case depth and hardness patterns are found by matching equipment parameters, these settings can be made consistent for a repeatable process across every part.
While the application described involves surface hardening, it is adaptable for other heat-treating operations that require progressive heating, such as annealing and tempering.